Investment In Automated Handling Improves Quality At Berkshire Labels
Posted: October 25, 2010
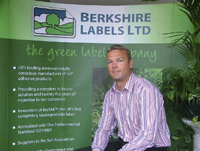
Paul Roscoe, Managing Director of the family business, is proud of his high efficiency plant that serves a portfolio of quality brand owners
'Lean and Green' is how Paul Roscoe describes Berkshire Labels, the 25-year old family business that he runs in Hungerford, Berkshire. The company, one of the premier converters of quality labels in the UK, is renowned for its ecological stance on production methods, and is proud of its programme of ongoing investment in all round efficiency.
"We re-invest around 10% of our annual turnover each year, which is a major commitment, but it brings rich dividends," explained Roscoe. In recent times, Berkshire Labels has installed a complete CtP system that has reduced plate-making times by 75%, and by eliminating solvent usage too, has delivered a better quality end product from a more eco friendly environment. Staff productivity has seen a dramatic improvement, according to Roscoe, who has lavish praise for his workforce of 45.
Printing is carried out on a bank of letterpress and flexo machines, the most modern of which are three 13" Mark Andy 2200 and LP3000 lines. The two older presses both have 8-colour capability, but the latest top spec 2200 XL model is a 6-colour machine fitted with a Martin Automatic MBS unwind/splicer. "Another 8-colour Mark Andy would have been the obvious choice, but when we evaluated the alternatives against our job portfolio, it became obvious that a 2200 offered the best ratio of investment to return, and that the money would be put to better use if we specified fewer colours but fitted the press with automated roll changing," he explained.
Four months on, the installation has already exceeded expectations by allowing continuous running with a noticeable improvement in press performance and print quality. One early job, explained Roscoe, which was estimated to take 90 - 100 hours to produce, was run off non stop in 60 hours, and yielded significant savings in material waste left on the cores. Set to splice with only 2 metres of substrate remaining in the reel, the Martin MBS has, in some cases, reduced wastage to as little as two A4 sheets of labels.
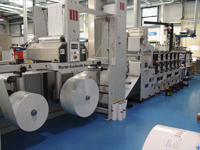
Berkshire Labels has linked a Martin Automatic MBS splicer to its new six-colour Mark Andy 2200XL press, and seen a marked improvement in print quality.
"We can run the press consistently close to its top speed of 155 m/min safe in the knowledge that there will be no drop in quality during roll changes. Working on three changes per hour, so 24 per shift, we are gaining an extra two hours production, added to which we waste less material. It's simple, really!" he said. Coupled with the latest GEW E-Brick UV system, Roscoe believes his latest 2200/MBS installation is one of the most environmentally efficient presses in the country.
Berkshire Labels sets its stall by its degree of commitment to eco-friendly work, and developed the BioTAK range of 'green' labels to raise industry standards. BioTAK labels are fully biodegradable by virtue of the substrates used and importantly the compostable adhesive. "Many companies claim to have to green credentials, but we decided to quantify ours by investment in techniques and technology," said Roscoe. Since launching, BioTAK has been well received by various sectors of the market, and given Berkshire a clear lead over its competitors. "We may not be the biggest, but we believe passionately that we are the best," he exclaimed.
With plans well advanced to develop an extra 6000 square foot unit onsite in Hungerford, and a re-organisation of the production floor to accommodate digital technology due to be installed before the year end, Paul Roscoe and his team are well set to grow the Group's business through the £10m turnover band. "This year we shall end up investing around 20% of sales value, and that includes new Esko and Digicon equipment as well as a digital press, along with the air-conditioned environment to go with it," he added.
The company has vibrancy about it, largely due to its talented and long serving staff. "They are our greatest asset and deserve the ongoing investment we make in their training and skill enhancement. We might be lean and green, but we're not mean!" he concluded.